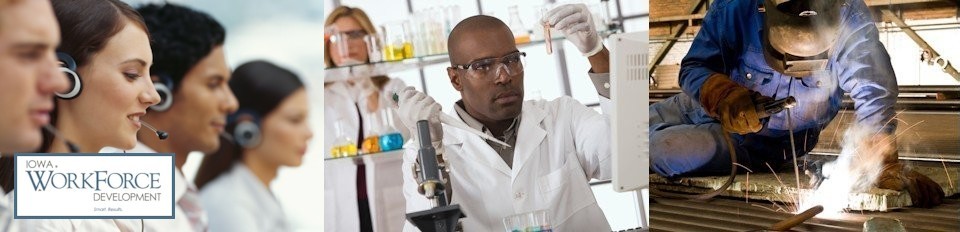
Job Information
Eaton Corporation Senior Quality Engineer in Davenport, Iowa
Eaton’s AER MSD Mission System Division is currently seeking a Senior Quality Engineer. This position will be located at our Davenport, IA facility.
The Davenport facility has approximately 900 employees and is a leader in the design, development, manufacture and delivery of Aerospace life support and safety systems components and services to the global aftermarket and OEM markets.
The expected annual salary range for this role is $80250.03 - $117700.04 a year.
Please note the salary information shown above is a general guideline only. Salaries are based upon candidate skills, experience, and qualifications, as well as market and business considerations.
What you’ll do:
• Participate in and/or perform various audit along with compiling corresponding reports when required.
• Assist with the implementation of quality processes, procedures, work instructions, standards and regulatory requirements.
• Conduct training on quality assurance concepts, tools and software.
• Serve as the Quality Point of Contact (POC) between the Operations and other quality functions.
• Manage customer and internal communications in a timely and professional manner, ensuring they are handled as required.
• Ensure lessons learned are applied to other programs and ensure processes are updated accordingly.
• Lead the monthly report outs as assigned.
• Provide support relative to the collection and analysis of quality data.
• Document and report concerns via internal tracking methods including but not limited to nonconformance records.
• Mentor IPT team members on requirements as needed.
• Ensures both customer and regulatory requirements are met.
• Support the adherence of business management system (BMS) processes by all functions.
• Interprets engineering drawings and specifications, customer quality requirements, and company quality requirements to ensure compliance with the customer's expectations.
• Perform Root Cause Corrective Action utilizing disciplined methodologies such as 8D to ensure effectiveness.
• Act as the functional project manager within the Quality team, managing the Quality deliverables and their completion to the project schedule and requirements to all projects as assigned.
• Witness and audit the building and testing of product as needed.
• Perform risk analyses and implement associated mitigations.
• Review and approve work instructions.
• Assemble and verify customer PPAP submissions prior to delivery to customers as required.
• Review and verify supplier PPAP submissions for acceptance as needed.
• Review all customer/program deliverables/activities and verify for their completeness.
• Participate in monthly/periodic reviews and present the quality status up to and including senior leadership as required.
• Perform all operations according to prescribed safety and environmental principles.
• Complete other duties, as assigned.
Qualifications:
Required (Basic) Qualifications:
• Bachelor’s degree in Engineering from an accredited institution.
• Minimum of three (3) years Quality or Manufacturing experience.
• Must be legally authorized to work in the United States without company sponsorship, now or in the future.
• This position requires use of information or access to hardware which is subject to the International Traffic in Arms Regulations (ITAR). All applicants must be U.S. persons within the meaning of ITAR. ITAR defines a U.S. person as a U.S. Citizen, U.S. Permanent Resident (i.e. 'Green Card Holder'), Political Asylee, or Refugee.
• No relocation benefit is being offered for this position. Only candidates within a 70-mile radius of Davenport, IA will be considered. Active-Duty Military Service member candidates are exempt from the geographical area limitation.
Preferred Qualifications:
• Minimum of five (5) years experience with AS9100/ISO9001 (aerospace), MIL-STD, ISO13485 (medical), or TS16949 (automotive).
• Minimum of three (3) years experience with Root Cause Analysis Tools, Lean Manufacturing, Statistical Process Control (SPC) and Lifecycle Management (LCM) experience.
• Minimum of three (3) years experience in reading and interpreting technical documents, including prints (GD&T), drawings, and engineering orders.
• Project/Program Management experience.
• Advanced Product Quality Planning (APQP) experience, including associated tools such as characteristics matrices, process flow diagrams, Failure Mode and Effects Analysis (FMEAs), Control Plans, Measurement System Analysis (MSA), and the Production Part Approval Process (PPAP).
Skills:
• Proficiency in Microsoft office tools such as Excel, PowerPoint, Outlook, Visio.
• Strong understanding of ASME Y14.5 standard - An understanding of budgets and the estimating process.
• Familiarity with regulatory requirements, Government/Military contracts, and Aerospace industry experience.
#LI-CB3
We are committed to ensuring equal employment opportunities for all job applicants and employees. Employment decisions are based upon job-related reasons regardless of an applicant's race, color, religion, sex, sexual orientation, gender identity, age, national origin, disability, marital status, genetic information, protected veteran status, or any other status protected by law.
Eaton considers qualified applicants regardless of criminal histories, consistent with local laws. To request a disability-related reasonable accommodation to assist you in your job search, application or interview process, please call us at 1-800-836-6345 to discuss your specific need. Only accommodation requests will be accepted by this phone number.
We know that good benefit programs are important to employees and their families. Eaton provides various Health and Welfare benefits as well as Retirement benefits, and several programs that provide for paid and unpaid time away from work. Click here (https://www.eaton.com/content/dam/eaton/company/careers/US%20Benefits%20updated%2010.24.22.pdf) for more detail: Eaton Benefits Overview. Please note that specific programs and options available to an employee may depend on eligibility factors such as geographic location, date of hire, and the applicability of collective bargaining agreements.
Eaton Corporation
-
- Eaton Corporation Jobs